Drum dryer (wood sawdust, chips, straw, grain, corn)
Drum Dryer SDD
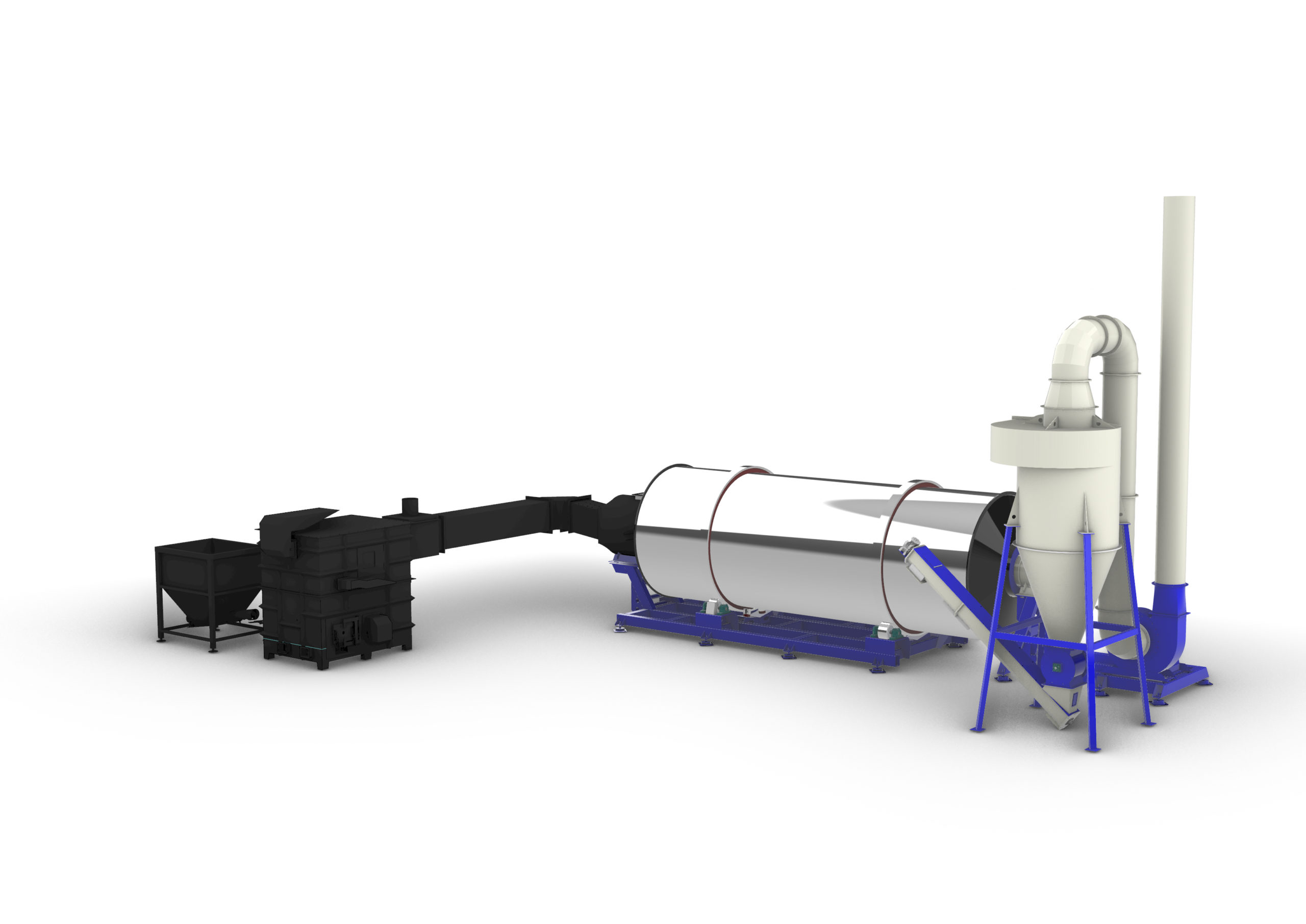
The set of device is designed for drying bulk materials for instance sawdust, wood shavings, wood chips, straw, grain, cereal stems, corn and other material. Performance, consumption of fuel and installed power depend on size and type of the dryer (see model variants SDD). The set of technological equipment – dryer of sawdust SDD consists of hot-air boiler with fuel reservoir, rolling cutter, hopper with auger, drying three-chambered steel isolated cylinder, exhaust fan, solid particles separator – cyclone, tourniquet with discharge conveyor.
The solid particles separator – cyclone with the exhaust fan ensure the outlet of steam and dust from the drying drum. Then the steam is brought out of the device by air technical pipes from the separator.The material in the drum is poured by rotation and moved to the exhaust chamber with the help of sliding blades. Dry sawdust is then exhausted from the cylinder to the separator by the exhaust fan and subsequently moved to the reservoir of dried material or press reservoir with the help of auger. Technology of the drum dryer and hot-air boiler works from the viewpoint process as one functional unit. The dryer is equipped by electro motors with gearboxes in the way to minimize the intensity of energy input during the operation of the device. Thus the dryer works in a very energy saving mode. The dryer is heated by boiler of its own construction designed only for this purpose. The boiler is fully automatized and woodchips, pellets or sawdust may be used as a fuel.
The dryer may work in a manual mode with the assistance of operators or automatically regulated by the operation system. The operation of the dryer depends on the assembled variant of the dryer and consist in supervision on the right operation of the individual devices, setting on the required temperature regulators of input and output temperatures, filling material into the fuel reservoir, controlling the level of material in dryer hoppers and basic maintenance. The set of device is equipped by safety components as are for example safety thermostat of output temperature, temperature sensor of fuel feeder and sensor of closing lid of fuel hopper. The drying drum is equipped by safety thermostat which shuts down the boiler and ventilator in the case the temperature is exceed. The whole system is controlled by touch panel where the technology is clearly graphically displayed.
Drying process
The set of drum dryer, rolling up auger, hot-air boiler, ventilator and conveyor works from the viewpoint process as one functional unit. The run of the whole set of device is controlled from the central electro switchboard which is equipped by PLC control unit which works with the transferred data from sensors and a thermocouple of the set. In relation to these data the control system of the switchboard edit the running of the whole set in order to achieve the required parameters during drying. There is a direct link between output temperature of flue gases from the boiler, input temperature of hot air into drying drum and output temperature of material. These parameters regulate the run of the whole set of device and performance of the dryer.
There is burning of fuel in the furnace which is filled by the auger from the fuel reservoir and the combustion is supported by primary air which is brought into the furnace under the grate and to side nozzles of the furnace with the help of boiler ventilator. Fuel supply into the furnace and amount of air are regulated automatically based on the thermocouple fitted in the furnace. Other gasification chamber is placed above the combustion chamber in which the gas combustion occurs and are created by burning of fuel in the furnace. Above this chamber there is a mixing chamber in which the secondary air is sucked. Residual gases are burnt out in this chamber and thus a complete combustion is occurred there. Suction of secondary air into the mixing chamber leads to reduction in temperature of flue gases and burn out of any sparks which are sucked into the combustion chamber and regulation chamber. Then the hot air is sucked into the dryer system from the combustion and regulation chamber with the help of main exhaust fan. The input temperature is automatically regulated with the help of suction valves which are controlled by servomotors in relation to set and required input temperature.
Drying material is dosed with the help of augers and according to the requirement of the control system into the drying drum into which the required hot air from the boiler is sucked. Material is poured by rotation in the drum and moved to the suction chamber with the help of sliding vanes. Then the dry sawdust is sucked from the cylinder by the exhaust fan to the centrifugal separator. The solid particles separator – cyclone with the exhaust fan ensure the exhaust of steam and dust from the drying drum and then steam is brought from the separator by the air-technical pipes out of device. Dried material is then separated from the steam with the help of dispenser – tourniquet and then discharged by the auger to the further processing or into the reservoir of dry material. In relation to moisture of input material which may be in range between 15% to 80% of moisture, the control system adjusts amount of dispensed material into the drum, adjusts the discharge of material, speed of drum rotation and regulates the boiler. The dryer may work in a manual mode with the assistance of operators or may be switched over to the automatic mode and then it is regulated by the control system.
After ignition of boiler by the manual mode (it is possible to set the performance of a blower and fuel feeder manually in percentage through the panel) and the boiler goes from the mode “heat up” into the mode “automatic operation” by heating up to the required temperature of about 250°C. Here the modulation of performance begins to work here. In case of increased demand on removing heat e.g. by increasing of performance of exhaust fan then the performance of boiler is also increased (amount of dosage of fuel and combustion air of burner are increased). The required output temperature from the boiler is being constantly controlled. At the time of firing up of the boiler there is a continuous heating of the drum of the dryer concurrently. Heating and warming up the whole system occur after about 30 minutes by the performance of fan to 15% and slow rotation of drum. If the output temperature from the dryer reaches 70°C then the performance of the fan is automatically increased. The system is stabilized and switched into the automatic mode during the drying process. The resulting output moisture of sawdust is kept on the required value during drying process. The performance of drying may be infinitely changed by the performance of transport ventilator. It is not needed to monitor input moisture of sawdust. On the basis of performance change of transport ventilator, performance of boiler is automatically changed in order to keep the required input temperature into the dryer. Performance of drying may be also increased by increase of required output temperature of the boiler but this negatively reflects in the following procession of pelleting where it causes degradation of lignin in sawdust at higher temperatures and thus the sawdust is debased and the process of granulation is difficult. The operation of the dryer depends on the assembled variant of the dryer and consist in supervision on the right operation of the individual devices, setting on the required temperature regulators of input and output temperatures, filling material into the fuel reservoir, controlling the level of material in dryer hoppers and basic maintenance.
Model variants
SDD frame version